Research
By exploring the interactions of enzymes and microorganisms with polymers, fibers and textile materials, we are working to help find solutions to urgent global challenges of CO2 removal, solid waste management and new product development while discovering fundamental new materials and mechanisms that combine the versatile attributes of textiles and biotechnology.
*********
Carbon Dioxide Removal
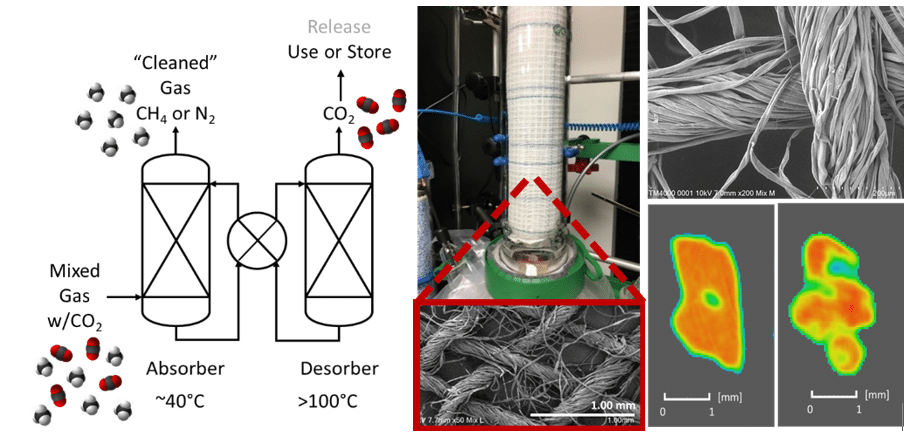
Lower cost, highly-efficient, scalable technologies for carbon capture from flue gas, industrial point sources and air are urgently needed to achieve reductions in atmospheric CO2 and a carbon pollution-free power sector by 2035 on the path to a net zero US economy by 2050, which is the goal of the 2021 Executive Order 14008 “Tackling the Climate Crisis at Home and Abroad.” We are developing a novel category of biocatalytic textile-based gas liquid contactors to increase CO2 capture efficiency and lower process complexity and cost.
We are also excited to be part of the Novo Nordisk Foundation funded Biocatalyst Interactions with Gases (BIG) Collaboration that aims to advance fundamental knowledge on three globally essential gas transformation reactions that are catalyzed in nature by enzymes: 1) carbon dioxide hydration to bicarbonate, catalyzed by carbonic anhydrase; 2) carbon dioxide reduction to formate, catalyzed by formate dehydrogenase; and, 3) nitrogen reduction to ammonium, catalyzed by nitrogenase.
*********
Textile Waste Circularity
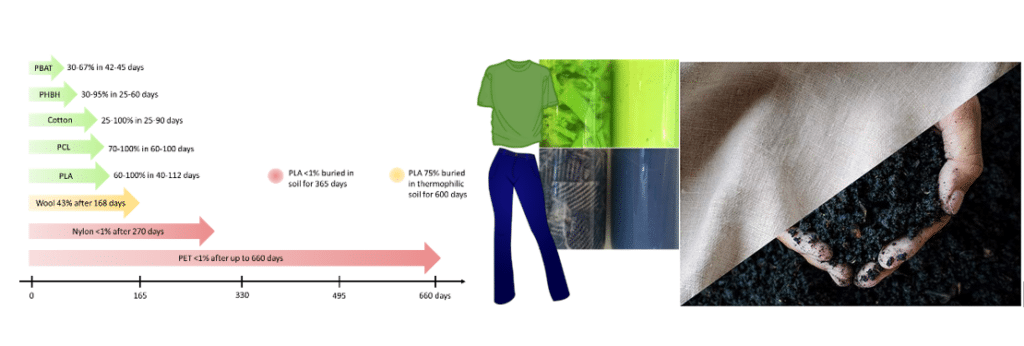
Let’s make the circular economy happen by converting waste textiles to valuable recyclable fibers and renewable fuel. Around 11 million tons of post-consumer textile waste (PCTW) are disposed of in U.S. landfills annually. This waste contains complex blends of natural and synthetic fibers that are difficult to mechanically separate, as well as dyes and other chemicals that interfere with reuse. By using mild enzymatic methods, we aim to divert PCTW from landfills by producing pumpable natural fiber slurries that can then be easily separated from non-degraded synthetic fibers, can be upgraded to value-added materials, can be converted to biofuels by anaerobic digestion, or can be mixed with compost to produce soil amendments.
*********
Accelerating Hemp
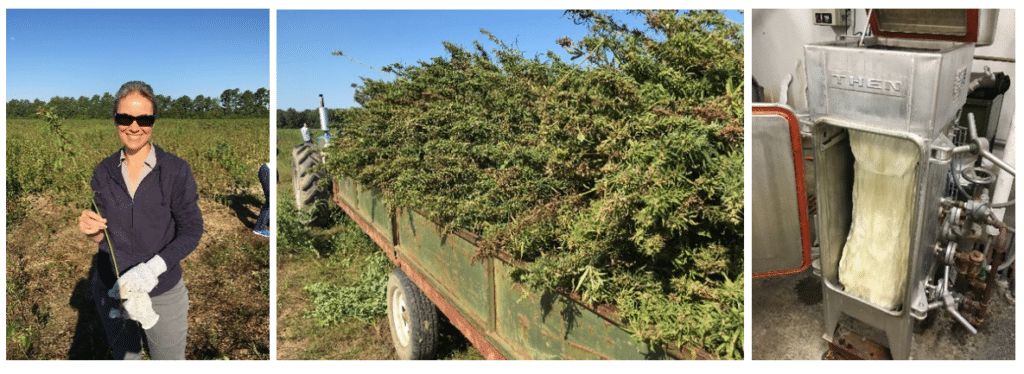
The global hemp (Cannabis sativa L.) products market is projected to grow from $4.5 billion in 2019 to $21 billion by 2028, increasing the supply of raw fiber that could be available for textiles as a sustainable raw material, but corresponding hemp fiber processes need to be established. Hemp plants are hardy, require minimal water or chemicals and diversify crops. However, efficient fiber separation is a current obstacle to producing textile-grade fibers. The US textile industry wants “cottonized” hemp, which requires converting long decorticated hemp strands to the right range of fiber bundle lengths, fineness and cleanliness to be processed on the short staple spinning equipment that dominates US textile manufacturing. Efficient and quantitative fiber grading measurements are also needed to bring the promise of textile hemp fiber to fruition.
*********
Biobased Materials
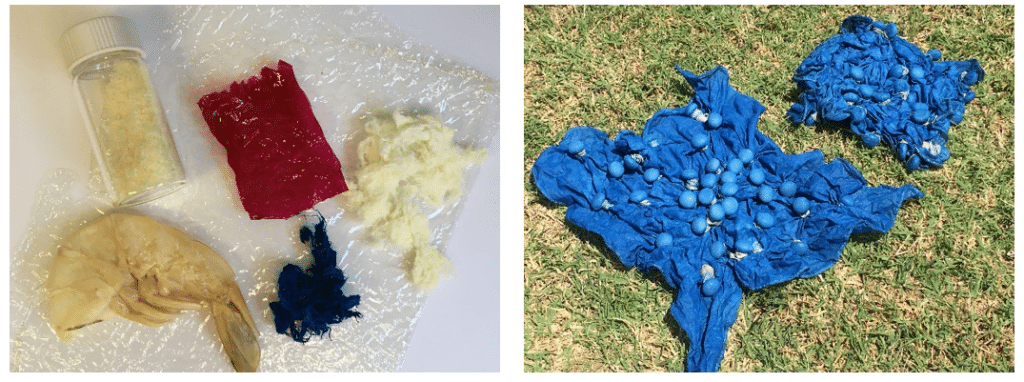
Nature’s amazing array of polymers, enzymes and colorants inspire our exploration of biobased materials for their high performance, multifunctional attributes and sustainable behaviors. Among these, cellulose, the most abundant polymer on the planet, is Nature’s gift to the textile industry. It has fascinating morphologies with versatile properties in its different forms and is both durable and biodegradable. The performance, properties and degradability of cellulose are central to many of our research efforts. Chitosan, the deacetylated derivative of chitin, the structural polysaccharide in crab and shrimp shells, is also an abundant polymer with a unique polycationic character at acidic conditions that makes it readily soluble in benign aqueous solvents, like vinegar. This easy solubility makes it possible to fabricate chitosan solutions into many different shapes and sizes – films, fibers, beads, particles – that can be re-solidified by adjusting to alkaline pH or can be used in the protonated form to bind securely to other materials – like cellulose. Learning about the chemical transformations of natural colorants like indigo encourages fresh thinking on how to reduce the impact of dyes and other chemicals applied to textiles. Enzymes, Nature’s protein-based catalysts, are essential to the creation and biodegradation of biobased materials, and they can also be harnessed to help improve the sustainability of many important commercial processes by increasing reaction efficiency, reducing water and chemical use, and saving energy.